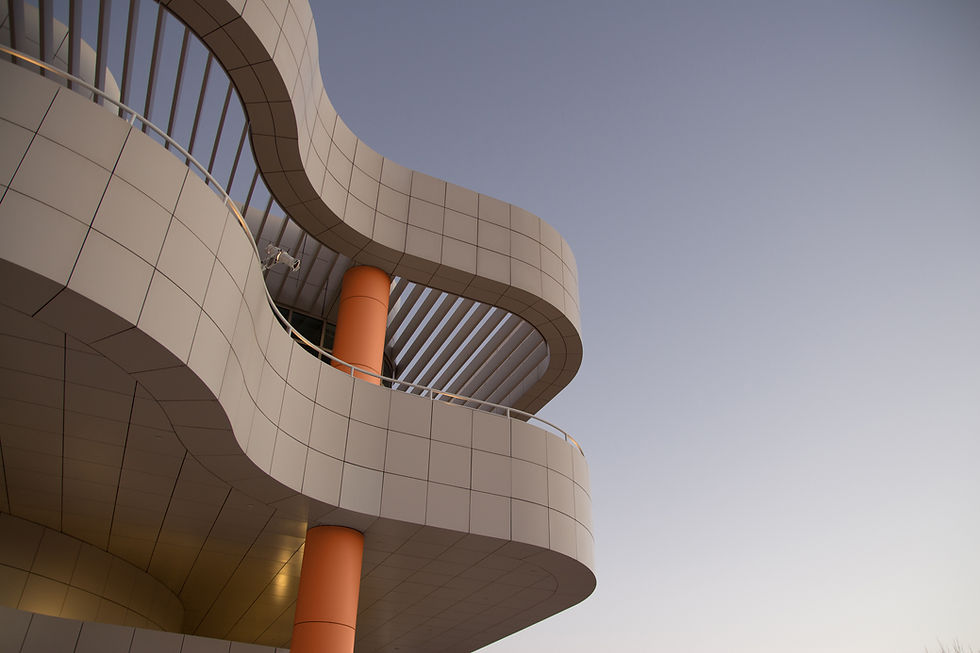
Additive Manufacturing and Injection Molding in the Medical Device Industry
0
0
The medical device industry is one of the most demanding sectors when it comes to manufacturing precision, quality, and compliance. With the rise of advanced manufacturing technologies, additive manufacturing (AM) and injection molding have emerged as two of the most impactful methods for producing medical devices. Each technology offers unique advantages, and in some cases, they can even complement one another to meet the diverse needs of the medical field. In this blog post, we’ll explore how these technologies are shaping the medical device industry and their respective benefits.

Additive Manufacturing in the Medical Device Industry
Additive manufacturing, commonly known as 3D printing, has revolutionized the medical device industry by enabling the production of highly customized and complex components. This technology builds parts layer by layer, allowing for unparalleled design flexibility and precision.
Key Benefits of Additive Manufacturing in Medical Devices
Customization and Personalization: Additive manufacturing excels in creating patient-specific devices, such as prosthetics, implants, and surgical guides. This level of customization is critical for improving patient outcomes and comfort.
Rapid Prototyping: Additive Manufacturing allows for quick production of prototypes, enabling medical device manufacturers to test and iterate designs faster than ever before. This accelerates the development process and reduces time to market.
Complex Geometries: Additive Manufacturing can produce intricate designs, such as lattice structures for implants, that are impossible to achieve with traditional manufacturing methods.
Cost-Effective for Low Volumes: For small production runs or highly specialized devices, additive manufacturing eliminates the need for expensive tooling, making it a cost-effective solution.
Applications of Additive Manufacturing in Medicine
Orthopedic Implants: Custom-fit implants for knees, hips, and other joints.
Surgical Instruments: Lightweight, ergonomic tools tailored to specific procedures.
Dental Devices: Crowns, bridges, and aligners designed for individual patients.
Bioprinting: Emerging applications include printing tissues and organs for research and transplantation.
While additive manufacturing offers incredible advantages, it is not always the best choice for mass production due to its slower production speeds and higher cost per unit for large volumes.
Injection Molding in the Medical Device Industry
Injection molding is a well-established manufacturing process that involves injecting molten material into a mold to create parts. It is particularly suited for high-volume production of medical devices and components.
Key Benefits of Injection Molding in Medical Devices
Scalability and Cost Efficiency: Injection molding is highly cost-effective for mass production. Once the mold is created, the cost per unit decreases significantly, making it ideal for producing large quantities of medical devices.
Material Versatility: This process supports a wide range of materials, including biocompatible plastics and resins that meet the stringent requirements of the medical industry.
Precision and Consistency: Injection molding ensures that every part produced is identical, which is critical for medical devices that require strict tolerances and reliability.
Sterilization Compatibility: Medical devices manufactured through injection molding can withstand various sterilization processes, ensuring patient safety and infection control.
Applications of Injection Molding in Medicine
Surgical Instruments: Scalpels, forceps, and other tools that require durability and precision.
Implants: Components like pacemaker casings and orthopedic screws.
Diagnostic Equipment: Housings and enclosures for medical devices such as blood analyzers and imaging machines.
Consumables: Syringes, IV connectors, and other disposable medical products.
While injection molding is excellent for high-volume production, its high upfront tooling costs make it less suitable for low-volume or highly customized parts.
Hybrid Solutions: Combining Additive Manufacturing and Injection Molding
In some cases, the best approach is to combine the strengths of both technologies. For example:
Prototyping with Additive Manufacturing: Use 3D printing to quickly create and test prototypes.
Scaling with Injection Molding: Once the design is finalized, transition to injection molding for mass production.
This hybrid approach allows manufacturers to benefit from the speed and flexibility of additive manufacturing during the design phase and the efficiency and scalability of injection molding for production.
Choosing the Right Technology for Your Medical Device: Additive Manufacturing and Injection Molding in the Medical Device Industry
The choice between additive manufacturing and injection molding depends on several factors, including:
Production Volume: Additive manufacturing is ideal for low-volume, customized parts, while injection molding is better suited for high-volume production.
Design Complexity: Additive Manufacturing excels at producing intricate and complex geometries, whereas injection molding is more limited in this regard.
Material Requirements: Injection molding offers a wider range of materials, including those that meet specific biocompatibility and sterilization standards.
Cost and Time: Additive Manufacturing reduces upfront costs and lead times for prototypes, while injection molding becomes more cost-effective at scale.
Conclusion
Both additive manufacturing and injection molding play vital roles in the medical device industry, offering unique advantages that cater to different needs. Additive manufacturing is driving innovation with its ability to produce customized, complex, and patient-specific devices, while injection molding remains the gold standard for high-volume production of reliable and durable components. By understanding the strengths of each technology, medical device manufacturers can choose the best approach—or even combine them—to meet the demands of this dynamic and critical industry.
At Paradigm Manufacturing, we specialize in both additive manufacturing and injection molding solutions for the medical device industry. Whether you need rapid prototyping, low-volume production, or large-scale manufacturing, we’re here to help you bring your medical innovations to life. Contact us today to learn more!