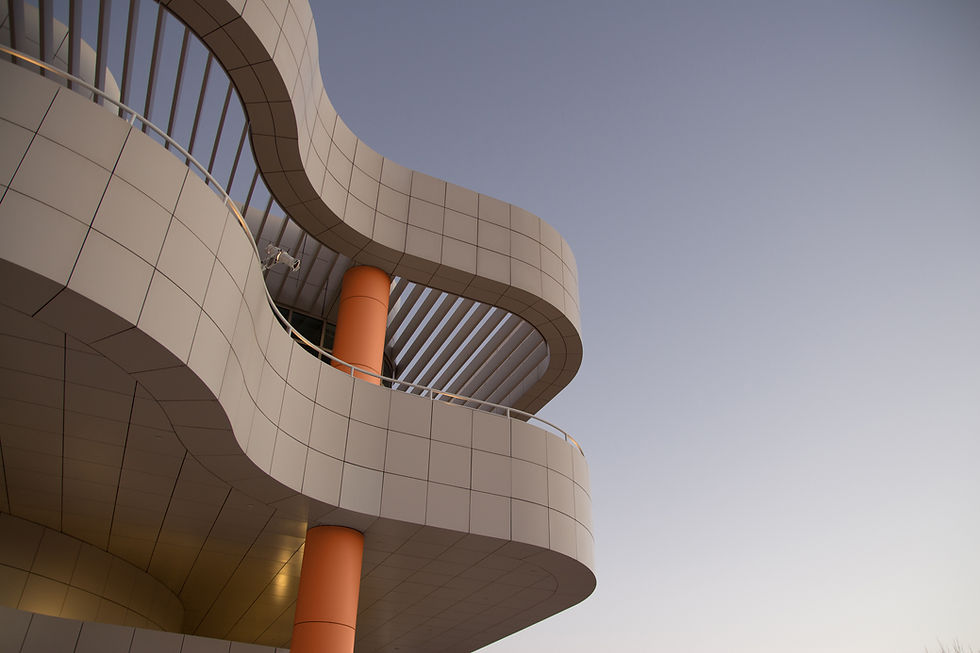
How Additive Manufacturing is Addressing Supply Chain Shortages
0
0
Supply chain disruptions have become a recurring challenge in recent years, impacting industries from healthcare and aerospace to consumer goods and automotive. Whether caused by global pandemics, geopolitical tensions, or natural disasters, these shortages highlight the vulnerabilities of traditional manufacturing and logistics systems. Amid these challenges, additive manufacturing (AM), also known as 3D printing, has emerged as a game-changing solution, offering companies a way to mitigate supply chain disruptions and maintain production continuity.

In this blog post, we’ll explore how additive manufacturing is helping businesses navigate supply chain shortages by enabling localized production, reducing dependency on global suppliers, and improving flexibility.
The Problem: Supply Chain Vulnerabilities: How Additive Manufacturing is Addressing Supply Chain Shortages
Traditional manufacturing relies heavily on centralized production and global supply chains. Components are often shipped across multiple countries before they are assembled into finished products. While this approach can optimize costs, it also creates significant vulnerabilities, such as:
Material Shortages: Delays in sourcing raw materials, such as metals, plastics, and semiconductors.
Transportation Disruptions: Shipping delays caused by port congestion, labor shortages, or rising fuel costs.
Single-Source Dependencies: Over-reliance on a single supplier or region (e.g., reliance on semiconductor production in East Asia).
Long Lead Times: Traditional tooling and manufacturing processes require weeks or months to produce parts, compounding delays when demand surges unexpectedly.
These challenges underscore the need for a more flexible and resilient manufacturing approach—and that’s where additive manufacturing comes in.
How Additive Manufacturing Solves Supply Chain Challenges
Additive manufacturing offers unique advantages that address the root causes of supply chain shortages. By enabling on-demand production, local manufacturing, and design flexibility, Additive manufacturing is transforming the way businesses handle disruptions.
1. On-Demand Production
Additive manufacturing eliminates the need for large inventories by enabling companies to produce parts only when they’re needed. Instead of waiting weeks for parts to be shipped from a supplier, businesses can print components on-site or at a nearby facility.
Example: During the early months of the COVID-19 pandemic, hospitals faced a critical shortage of personal protective equipment (PPE) and ventilator parts. Additive manufacturing was used to produce face shields, masks, and even ventilator components on demand, helping to bridge the gap until traditional supply chains recovered.
2. Localized Manufacturing
Additive manufacturing allows companies to establish decentralized production hubs closer to their end users. By shortening the supply chain, businesses can reduce dependency on distant suppliers and minimize the risks associated with transportation disruptions.
Example: Automotive manufacturers are using additive manufacturing to produce spare parts locally, reducing lead times for critical components and ensuring that vehicles can be repaired without waiting for overseas shipments.
3. Faster Lead Times
Unlike traditional manufacturing, which requires extensive tooling and setup, additive manufacturing can produce parts directly from a digital design file. This drastically reduces lead times, allowing companies to respond quickly to demand spikes or unexpected shortages.
Example: Aerospace companies use additive manufacturing to produce lightweight, complex components for aircraft during supply chain bottlenecks, ensuring that production schedules stay on track.
4. Reduced Tooling Dependencies
Traditional manufacturing often requires custom molds, dies, and tooling, which can take weeks or months to produce. Additive manufacturing eliminates the need for tooling in many cases, allowing manufacturers to bypass delays associated with tool fabrication.
Example: Injection molding typically requires expensive molds, but additive manufacturing can be used to produce short-run parts or even the molds themselves, accelerating production timelines.
5. Material Efficiency
Additive manufacturing is inherently material-efficient, using only the material needed to build the part layer by layer. This reduces waste and alleviates the impact of raw material shortages.
Example: Metal 3D printing in industries like aerospace and medical allows manufacturers to produce high-performance parts with minimal material waste, reducing dependency on scarce raw materials.
6. Design Flexibility
Additive manufacturing allows for rapid design iteration and the production of complex geometries that traditional manufacturing cannot achieve. This flexibility enables companies to adapt designs to available materials or alternative suppliers quickly.
Example: Medical device manufacturers used 3D printing to redesign components for ventilators during supply chain shortages, replacing hard-to-source materials with locally available alternatives.
Industries Benefiting from Additive Manufacturing During Supply Chain Shortages
1. Healthcare
Challenge: Shortages of ventilators, PPE, and medical device components.
Additive manufacturing Solution: Rapid production of ventilator parts, face shields, and implants using biocompatible materials.
2. Automotive
Challenge: Supply chain delays for spare parts and components.
Additive manufacturing Solution: On-demand production of spare parts and localized manufacturing hubs to reduce lead times.
3. Aerospace
Challenge: Delays in sourcing lightweight, complex components for aircraft.
Additive manufacturing Solution: Production of custom, high-performance parts using metal 3D printing technologies.
4. Consumer Goods
Challenge: Long lead times for mass-produced goods.
Additive manufacturing Solution: Customization and small-batch production to meet demand during global disruptions.
Challenges of Scaling Additive Manufacturing
While additive manufacturing offers numerous advantages, there are challenges that businesses must address to fully leverage its potential:
Material Limitations: Not all materials are currently suitable for additive manufacturing, and some additive manufacturing-compatible materials may still face shortages.
Cost Considerations: While additive manufacturing reduces tooling costs, the cost per unit can be higher than traditional methods for large-scale production.
Skill Gap: additive manufacturing requires specialized expertise in design, materials, and machine operation, which can be a barrier for some companies.
Regulatory Compliance: In industries like healthcare and aerospace, additive manufacturing parts must meet strict certification standards, adding complexity to the process.
Despite these challenges, advancements in additive manufacturing technology, materials, and processes are making it easier for businesses to adopt this innovative approach.
Looking Ahead: Additive Manufacturing as a Long-Term Solution
Additive manufacturing is no longer just a tool for prototyping—it’s becoming a critical component of modern supply chain strategies. As companies seek to build more resilient and agile operations, additive manufacturing provides a way to:
Reduce dependency on global suppliers.
Respond quickly to disruptions.
Innovate with new designs and materials.
While it may not fully replace traditional manufacturing methods, additive manufacturing is a powerful complement that helps bridge gaps and ensure production continuity during crises. As supply chains continue to face challenges, businesses that embrace additive manufacturing will be better positioned to adapt and thrive.
Conclusion
Supply chain shortages have forced industries to rethink traditional manufacturing and logistics strategies. Additive manufacturing has emerged as a flexible and innovative solution, enabling on-demand production, localized manufacturing, and rapid response to disruptions. By integrating additive manufacturing into their operations, companies can build more resilient supply chains and stay competitive in an ever-changing global market.
At Paradigm Manufacturing, we specialize in providing additive manufacturing solutions to help businesses overcome supply chain challenges. Whether you need rapid prototyping, small-batch production, or support for large-scale operations, we’re here to help. Contact us today to learn how additive manufacturing can strengthen your supply chain and future-proof your production!