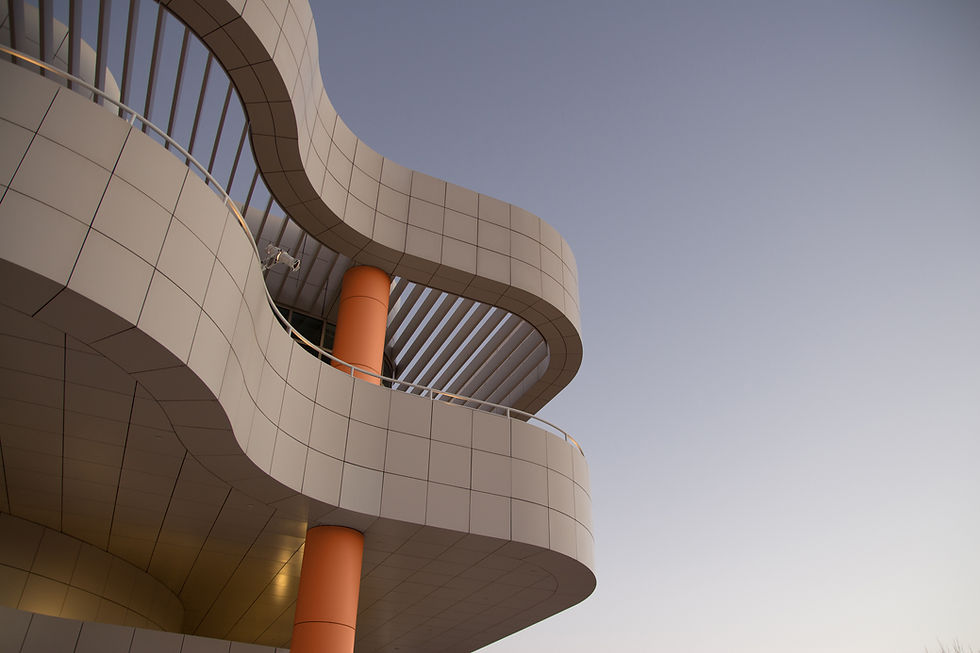
The Benefits of Hybrid 3D Printing and Injection Molding Solutions
1
4
In the world of manufacturing, 3D printing and injection molding are often seen as competing technologies. However, they don’t have to be an either/or proposition. By combining the strengths of both processes, manufacturers can unlock a powerful hybrid solution that offers the best of both worlds. This approach is particularly valuable for industries that require flexibility, speed, and cost-efficiency in production. In this blog post, we’ll explore the benefits of hybrid 3D printing and injection molding solutions and how they are transforming modern manufacturing.

What is a Hybrid 3D Printing and Injection Molding Solution?
A hybrid solution leverages the unique advantages of both 3D printing and injection molding to optimize the manufacturing process. Traditionally, 3D printing has been used for prototyping, while injection molding has been the go-to method for high-volume production. However, advancements in additive manufacturing have made it possible to integrate these two technologies in innovative ways. For example:
3D printing can be used to create molds for injection molding, enabling faster and more cost-effective tooling for small production runs.
Injection molding can complement 3D printing by producing high-quality, durable parts at scale after prototypes have been validated through additive manufacturing.
This hybrid approach allows manufacturers to take advantage of the speed and flexibility of 3D printing while benefiting from the efficiency and scalability of injection molding.
Key Benefits of Hybrid Manufacturing
1. Faster Time to Market
One of the most significant advantages of hybrid manufacturing is the ability to accelerate product development. With 3D printing, manufacturers can quickly produce prototypes and iterate designs without the need for expensive and time-consuming tooling. Once the design is finalized, injection molding can be used to produce parts at scale, significantly reducing lead times.
2. Cost Savings for Low-Volume Production
Injection molding is traditionally associated with high upfront costs due to the need for custom molds. However, by using 3D printing to create molds, manufacturers can reduce these initial expenses. This is particularly beneficial for low-volume production runs, where the cost of traditional tooling might be prohibitive. Hybrid solutions also allow for on-demand mold fabrication, eliminating the need for large inventories and reducing waste.
3. Design Flexibility
3D printing offers unparalleled design freedom, enabling the creation of complex geometries and intricate details that would be difficult or impossible to achieve with traditional injection molding. By combining this capability with injection molding, manufacturers can produce parts that are both highly customized and durable. For instance, 3D printing can be used to create molds with intricate internal features, which are then used in the injection molding process to produce high-quality parts with consistent finishes.
4. Improved Material Options
While 3D printing materials are expanding, they are still more limited compared to the wide range of materials available for injection molding. A hybrid approach allows manufacturers to take advantage of the material versatility of injection molding while still benefiting from the rapid prototyping capabilities of 3D printing.
5. Scalability
Hybrid manufacturing bridges the gap between prototyping and mass production. Manufacturers can use 3D printing to validate designs and produce small batches, then transition to injection molding for larger production runs. This scalability ensures that the manufacturing process remains efficient and cost-effective at every stage of the product lifecycle.
Applications of Hybrid Manufacturing
Hybrid 3D printing and injection molding solutions are being adopted across a wide range of industries, including:
Aerospace: Lightweight, complex components can be prototyped with 3D printing and then mass-produced using injection molding for durability and consistency.
Medical Devices: Custom molds created with 3D printing enable the production of small batches of medical components, such as surgical tools or implants, with injection molding ensuring biocompatibility and precision.
Consumer Goods: Hybrid solutions allow for rapid prototyping of new product designs, followed by efficient mass production to meet market demand.
Challenges and Considerations
While hybrid manufacturing offers numerous benefits, it’s important to consider the following challenges:
Material Compatibility: Not all 3D printing materials are suitable for creating molds for injection molding, so careful material selection is essential.
Durability of 3D Printed Molds: For high-volume production, traditional metal molds may still be required, as 3D printed molds may wear out more quickly.
Process Integration: Successfully combining 3D printing and injection molding requires expertise in both technologies to ensure seamless integration.
Despite these challenges, advancements in additive manufacturing and tooling technologies are making hybrid solutions more accessible and practical for a wide range of applications.
Conclusion
Hybrid 3D printing and injection molding solutions are revolutionizing the manufacturing landscape by combining the strengths of two powerful technologies. This approach offers faster time to market, cost savings, design flexibility, and scalability, making it an ideal choice for industries that demand innovation and efficiency. At Paradigm Manufacturing, we specialize in both 3D printing and injection molding, and we’re here to help you harness the power of hybrid manufacturing for your next project. Contact us today to learn more about how we can help you achieve your production goals!