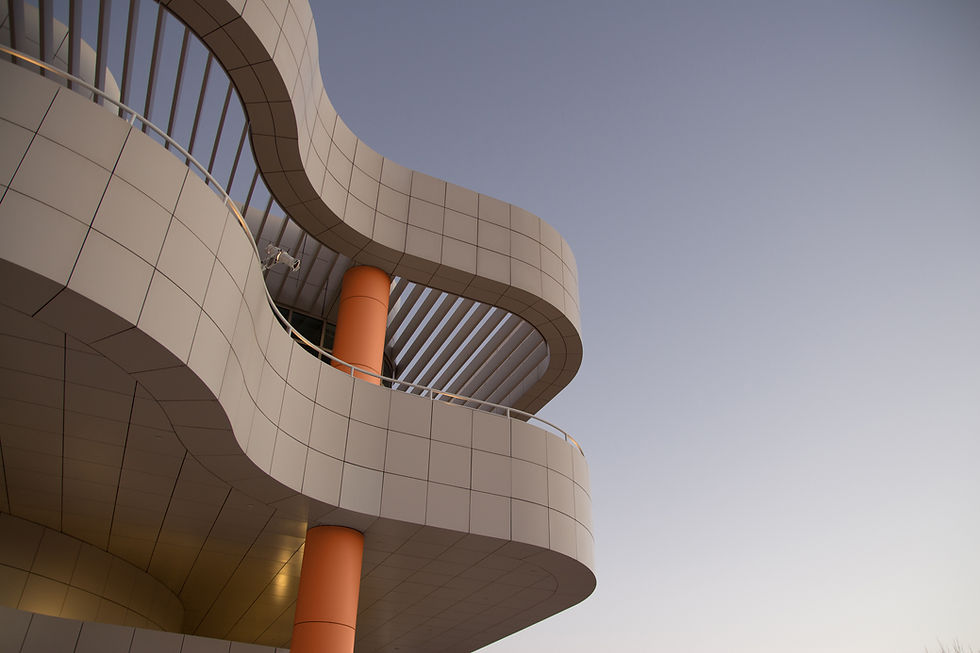
Using Additive Manufacturing and Injection Molding to Create GLP-1 Medication Devices
0
3
The demand for GLP-1 medication devices, such as self-administered injectors, is growing rapidly as these devices play a critical role in managing type 2 diabetes and obesity. GLP-1 (glucagon-like peptide-1) medications help regulate blood sugar levels, promote weight loss, and improve metabolic health, making them essential tools in modern healthcare. However, manufacturing these devices requires a balance between precision, scalability, and cost-efficiency to meet the demands of patients and healthcare providers.

By using Additive Manufacturing and Injection Molding to Create GLP-1 Medication Devices, manufacturers can streamline the production process, reduce costs, and create innovative, patient-centric designs. In this blog post, we’ll explore how these two powerful technologies complement each other in the development and production of GLP-1 medication devices.
Key Requirements of GLP-1 Medication Devices
GLP-1 medication devices, such as pen injectors or auto-injectors, must meet strict standards to ensure safety, accuracy, and ease of use. Some of the key requirements include:
Precision Dosage Delivery: Devices must consistently deliver the correct amount of medication.
Ease of Use: Design must accommodate patients with limited dexterity or experience with injectable devices.
Durability and Reliability: Components must withstand repeated use (for reusable devices) or provide consistent performance for single-use devices.
Scalability: The production process must meet the demand for millions of units while maintaining quality.
Regulatory Compliance: Devices must meet stringent healthcare regulations, such as FDA and ISO standards.
Meeting these requirements demands a flexible and efficient manufacturing strategy, which is where additive manufacturing and injection molding come in.
The Role of Additive Manufacturing (AM) in GLP-1 Device Production
Additive manufacturing, or 3D printing, is transforming the early stages of device development and even aspects of small-scale production. Here’s how it contributes to creating GLP-1 medication devices:
1. Rapid Prototyping
During the design phase, additive manufacturing allows manufacturers to quickly produce prototypes of GLP-1 devices for testing and iteration. This is crucial for refining key features such as:
Ergonomic design for patient usability.
Internal mechanisms for accurate dosage delivery.
Needle housings and safety mechanisms.
Prototyping with additive manufacturing reduces the time and cost associated with traditional prototyping methods, enabling faster innovation.
2. Design Complexity
3D printing can create intricate and complex geometries that traditional manufacturing methods cannot achieve. For GLP-1 devices, this might include:
Internal channels for medication flow.
Lattice structures to reduce weight without compromising strength.
Custom grips and textures to improve usability.
This design freedom allows manufacturers to optimize devices for performance and patient comfort.
3. Cost-Effective Low-Volume Production
For small batches, such as devices for clinical trials or custom solutions for specific patient groups, additive manufacturing eliminates the need for expensive tooling. This makes it an ideal solution for low-volume production.
4. Material Testing
3D printing enables manufacturers to test various materials, including biocompatible plastics, to ensure that the final product meets regulatory and performance requirements.
The Role of Injection Molding in GLP-1 Device Production
Once the design of the GLP-1 medication device has been finalized and validated, manufacturers turn to injection molding for large-scale production. Injection molding remains the gold standard for producing medical devices due to its efficiency, scalability, and precision.
1. High-Volume Production
Injection molding is ideal for producing millions of identical parts with consistent quality. This scalability is essential for GLP-1 devices, which are in high demand globally.
2. Cost Efficiency
While the initial cost of creating molds is high, injection molding becomes highly cost-effective at scale. The cost per unit decreases significantly as production volume increases, making it the preferred method for mass production.
3. Material Versatility
Injection molding supports a wide range of medical-grade plastics, including materials that are:
Biocompatible.
Sterilizable.
Durable enough to withstand repeated use or transportation.
This versatility ensures that GLP-1 devices meet safety and regulatory requirements.
4. Precision and Consistency
Injection molding ensures that every component of the device—such as housings, plungers, caps, and dosage mechanisms—is manufactured to tight tolerances. This precision is critical for the reliability and functionality of medical devices.
5. Smooth Finishes
Injection molding produces parts with smooth, professional finishes, reducing the need for post-processing. This is particularly important for patient-facing components of GLP-1 devices, where comfort and aesthetics matter.
The Hybrid Approach: Combining Additive Manufacturing and Injection Molding: Using Additive Manufacturing and Injection Molding to Create GLP-1 Medication Devices
By integrating additive manufacturing and injection molding, manufacturers can optimize every stage of the production process. Here’s how the hybrid approach works for GLP-1 medication devices:
1. Prototyping and Design Validation
Use additive manufacturing to create and test prototypes quickly and cost-effectively.
Iterate designs based on user feedback or performance testing.
2. Tooling with Additive Manufacturing
In some cases, 3D printing can be used to produce molds or mold inserts for short production runs, reducing tooling costs.
3. Scaling with Injection Molding
Transition to injection molding for mass production once the design is finalized.
Leverage the cost-efficiency and scalability of injection molding to produce millions of units.
4. Customization with Additive Manufacturing
For niche markets or specific patient needs, continue using additive manufacturing for small-batch production of customized devices or components.
This hybrid approach ensures that manufacturers can innovate rapidly during the design phase while maintaining efficiency and quality during large-scale production.
Challenges and Considerations
While additive manufacturing and injection molding offer significant benefits, there are challenges to address:
Material Compatibility: Ensuring that materials used in 3D printed prototypes closely resemble those used in injection-molded components is essential for accurate testing.
Regulatory Compliance: Both processes must adhere to strict healthcare regulations, which can add complexity to production.
Tooling Costs: For highly complex designs, creating molds for injection molding may still require significant investment.
Despite these challenges, advancements in both technologies are making it easier to integrate them into medical device manufacturing.
Conclusion
The production of GLP-1 medication devices requires a manufacturing strategy that balances precision, scalability, and cost-efficiency. By combining the strengths of additive manufacturing and injection molding, manufacturers can create high-quality devices that meet the needs of patients and healthcare providers alike. Additive manufacturing accelerates prototyping and customization, while injection molding ensures efficiency and consistency at scale.
At Paradigm Manufacturing, we specialize in leveraging both additive manufacturing and injection molding to help you bring your medical devices to market. Whether you need rapid prototyping, small-batch production, or large-scale manufacturing, we have the expertise and technology to support your goals. Contact us today to learn more about how we can help you produce innovative and reliable GLP-1 medication devices!